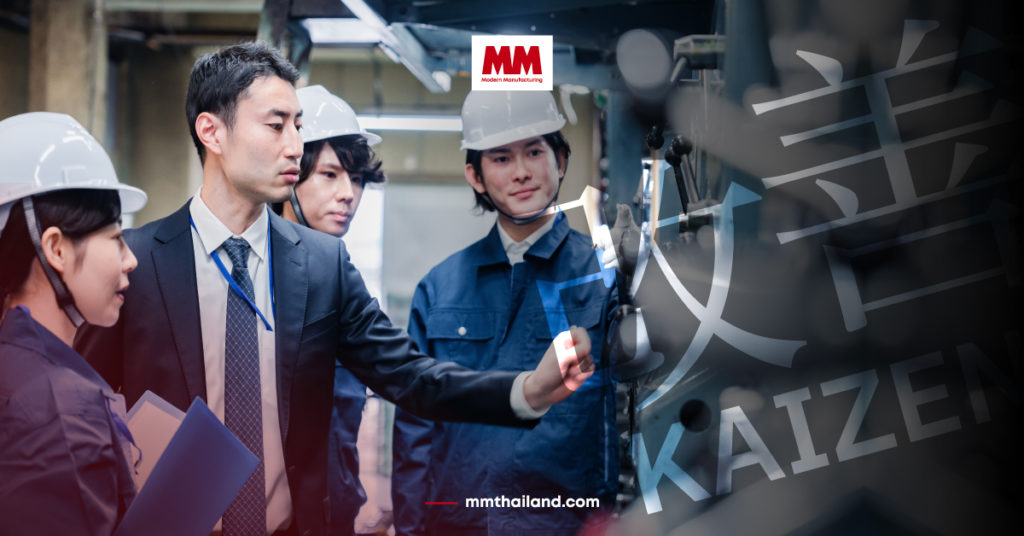
ทุกวันนี้เชื่อว่าผู้ประกอบการหลาย ๆ ท่านต่างก็สนใจและอยากที่จะมองหาแนวคิดในการทำงานที่มีประสิทธิภาพเข้ามาช่วยให้โรงงานของตัวเองสามารถลดต้นทุนและปรับปรุงคุณภาพในการผลิตให้เพื่อให้สามารถแข่งขันกับคู่แข่งในอุตสาหกรรมเดียวกันได้อย่างมั่นคง
- รู้หรือไม่ ? ว่า AI สามารถเสริม Productivity ในโรงงานได้ !
- รายงานเผย ทำงานกับหุ่นยนต์ส่งผลให้มนุษย์ขี้เกียจมากขึ้นแทน !
- 4 ประเด็นสำคัญในการรับมือความท้าทายแห่งอนาคตที่ CEO ต้องรู้!
แต่การจะนำเอาแนวคิดใหม่ ๆ เข้ามาใช้ในโรงงานนั้น บางครั้งโรงงานของคุณก็อาจจะเจอกับความท้าทายหลายอย่าง ไม่ว่าจะเป็นการต้านทานต่อการเปลี่ยนแปลงจากพนักงาน การขาดต้นทุนและทรัพยากรที่เพียงพอ หรือการขาดความรู้และความเข้าใจในแนวคิดเหล่านั้น
วันนี้ Modern Manufacturing จึงอยากพาทุกท่านมาทำความรู้จักกับวิธีการบริหารจัดการโรงงานให้มีประสิทธิผลที่ทำได้ง่ายและไม่ต้องใช้ต้นทุนสูงด้วยแนวคิดของการพัฒนาอย่างต่อเนื่องสไตล์ญี่ปุ่นอย่าง ‘Kaizen’ ที่ตั้งอยู่บนพื้นฐานความเชื่อว่าทุกสิ่งสามารถปรับปรุงได้ และไม่มีสิ่งใดจะคงสภาพที่เป็นอยู่ไปได้ตลอดเวลา
Kaizen แนวคิดของการเปลี่ยนแปลง
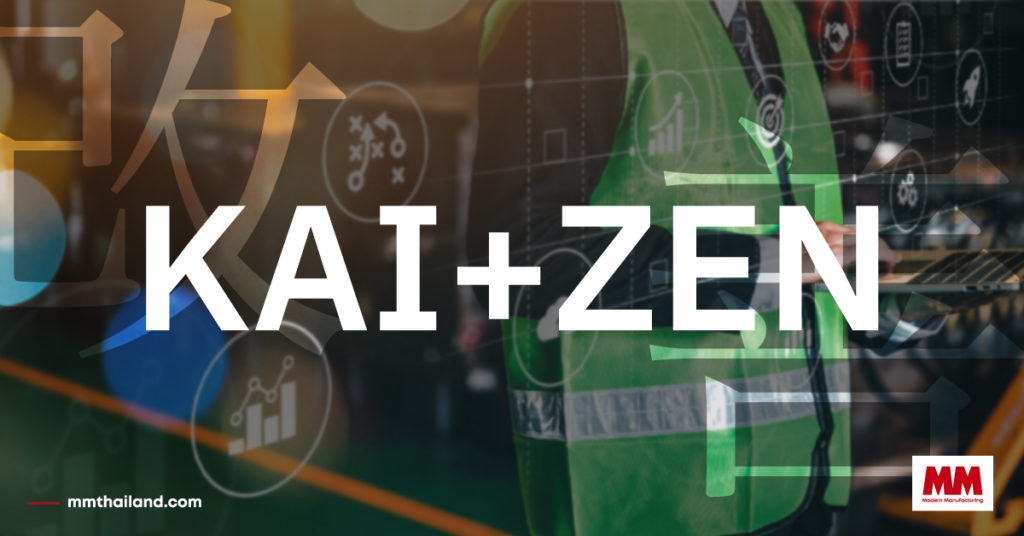
คำว่า Kaizen นั้นมาจากคำว่า ‘Kai’ (改) ซึ่งแปลว่า การเปลี่ยนแปลงหรือการแก้ไข และคำว่า ‘Zen’ (善) ซึ่งแปลว่า ดีขึ้นหรือดีงาม รวมกันออกมาเป็นคำว่า ‘Kaizen’ ที่แปลว่า “การเปลี่ยนแปลงเพื่อสิ่งที่ดีขึ้น” ซึ่งแนวคิดแบบ Kaizen นั้นก็เป็นแนวคิดที่ถือเกิดขึ้นมากว่า 1,300 ปีแล้วในประเทศญี่ปุ่น และเป็นที่นิยมอย่างมากในยุคสมัยเอโดะ (ปีค.ศ. 1603 – 1867)
การทำงานแบบ Kaizen ในโรงงานนั้นมีหัวใจสำคัญอยู่ที่ ‘การปรับปรุงอย่างต่อเนื่อง’ โดยเน้นไปที่การปรับเปลี่ยนทีละเล็กทีละน้อยเพื่อเพิ่มประสิทธิภาพและลดของเสียในกระบวนการผลิตลงผ่านการทำงานร่วมกันของพนักงานทุกคนในองค์กร เปลี่ยนรูปแบบการทำงานให้น้อยลงแต่มีประสิทธิภาพมากขึ้น ทำให้เกิดความสะดวกสบายและช่วยยกระดับคุณภาพชีวิตของพนักงานให้สูงขึ้นตามไปด้วย
ข้อดีที่ควรรู้ของแนวคิด Kaizen
สำหรับข้อดีของการนำแนวคิด Kaizen มาใช้ในโรงงานเมื่อเทียบกับแนวทางการปรับปรุงคุณภาพอื่น ๆ นั้นก็คือการไม่จำเป็นต้องใช้เงินลงทุนจำนวนมาก แต่สามารถสร้างผลลัพธ์ที่ยิ่งใหญ่และเห็นผลได้จากการเปลี่ยนแปลงเล็ก ๆ น้อย ๆ ในกระบวนการทำงาน ซึ่งจะเกิดขึ้นได้ผ่านการเปิดโอกาสให้พนักงานทุกคนตั้งแต่นายช่างและวิศวกรใน Shop floor ไปจนถึงผู้จัดการและผู้บริหารได้มีส่วนร่วมในการออกความคิดเห็นและแก้ไขปัญหาที่เกิดขึ้นจากการร่วมมือกันของทุกคนในองค์กร
การนำแนวคิดแบบ Kaizen มาปรับใช้ให้เกิดผลสำเร็จได้นั้นจะช่วยให้โรงงานสามารถได้รับผลประโยชน์ต่าง ๆ เหล่านี้ได้ ไม่ว่าจะเป็น
- เพิ่มผลผลิตและประสิทธิภาพในการทำงาน
- ลดของเสียในสายการผลิต
- ยกระดับคุณภาพของผลิตภัณฑ์
- ลดต้นทุนและประหยัดเวลาในการทำงาน
- ปรับปรุงความปลอดภัยในโรงงาน
- เพิ่มผลกำไรและความพึงพอใจของลูกค้า
‘เลิก ลด เปลี่ยน’ เริ่มต้นทำ Kaizen ง่าย ๆ ด้วยหลักการเหล่านี้

สำหรับโรงงานที่อยากเริ่มใช้แนวคิด Kaizen นั้น หลักการสำคัญที่ควรนำไปใช้ก็ได้แก่เรื่องของการ เลิก ลด เปลี่ยน (Stop, Reduce, Change) ปัจจัยต่าง ๆ ที่กำลังทำให้โรงงานและสายการผลิตของคุณต้องเสียประสิทธิภาพในการทำงานไป
- การ เลิก ในที่นี้หมายถึงการเลิกหรือการตัดขั้นตอนการทำงานแบบเดิม ๆ ที่ไม่มีความจำเป็นออกเพื่อลดขั้นตอนการทำงานที่สิ้นเปลืองทรัพยากรอย่างเวลา กำลังคน และวัตถุดิบ เช่นการลดขั้นตอนในการผลิตจาก 5 ลงเหลือ 3 ขั้นตอน แต่เพิ่มประสิทธิภาพในการผลิตให้ดีขึ้นแทนส่วนที่ลดไป
- การ ลด หมายถึงการลดความซ้ำซ้อนหรือความยุ่งยากในการทำงานที่ไม่ทำให้เกิดประโยชน์ และลดกิจกรรมที่ใช้ทรัพยากรมากเกินไปออกจากการทำงาน อย่างการลดเวลาในการประกอบชิ้นงานด้วยการปรับปรุงกระบวนการผลิตให้กลายเป็นระบบอัตโนมัติแทนการใช้แรงงานมนุษย์
- การ เปลี่ยน หมายถึงการปรับเปลี่ยนหรือปรับปรุงกระบวนการทำงานเพื่อเพิ่มประสิทธิภาพหรือแก้ไขปัญหาที่เกิดขึ้น เช่นการเปลี่ยนการจัดเก็บวัตถุดิบจากการใช้กล่องพลาสติกมาเป็นชั้นวางที่มีการจัดเรียงเป็นระบบ เพื่อให้ง่ายต่อการค้นหาและหยิบใช้งานนั่นเอง
นอกจากหลักการเบื้องต้นที่ว่ามาแล้ว การทำ Kaizen ยังเกิดขึ้นได้จากการใช้กลยุทธ์ 3MU (Muda/Mura/Muri) ที่มุ่งเน้นไปที่การการลดต้นทุนและกำจัดความสูญเปล่าเข้ามาทำให้โรงงานของคุณสามารถเปลี่ยนแปลงกระบวนการทำงานให้มีประสิทธิภาพมากขึ้นได้ก่อนจะค่อย ๆ ทำการปรับเปลี่ยนเข้าสู่แนวคิด Kaizen ซึ่งนอกจากนี้แล้วการนำเอาหลักการอื่น ๆ อย่าง 5S และ 4M เข้ามาเสริม ก็ถือเป็นองค์ประกอบสำคัญที่จะช่วยให้โรงงานสามารถนำเอาแนวคิด Kaizen มาใช้ให้เกิดผลได้สำเร็จจริง
การทำงานแบบ Kaizen ในโรงงานจะช่วยพัฒนาทั้งบุคลากรและวิธีการทำงานให้เกิดประสิทธิภาพและช่วยให้โรงงานสามารถสร้างการเจริญเติบโตอย่างยั่งยืนได้สำเร็จ โรงงานที่นำเอาแนวคิด Kaizen มาใช้ได้อย่างต่อเนื่องและสม่ำเสมอนั้นจะสามารถรักษาความสามารถในการแข่งขันและเพิ่มคุณค่าให้กับทั้งองค์กรและตัวพนักงานได้เป็นอย่างมาก รู้อย่างนี้แล้วก็อย่าลืมลองนำเอาแนวคิดดี ๆ แบบนี้ไปลองปรับใช้ในโรงงานของตัวเองกันดูนะครับ